Unlocking Effectiveness: The Benefits of Tailored Formed Processes
In today's competitive manufacturing landscape, efficiency and precision are critical. One standout solution that has gained considerable attention is custom injection molding. This process allows manufacturers to create exceptionally tailored and personalized products that meet unique requirements. Through custom injection molding, organizations can optimize production, minimize waste, and ensure greater quality standards, differentiating themselves from the competition.
This technique is not just about creating a product; it's about enhancing the complete manufacturing process. With the potential to produce detailed shapes and designs with incredible accuracy, firms can achieve greater flexibility in their product. In this article explores the myriad advantages of this method, showcasing how it can unlock new dimensions of efficiency and innovation in different fields.
What does Custom Injection Molding?
This process of custom injection molding is a technique used to create parts by infusing molten material into a bespoke mold. This method allows for high accuracy and consistency, making it a popular option for producing intricate designs and large quantities of items. The process can utilize multiple materials, such as synthetics, alloys, and composites, allowing manufacturers to tailor the final product to specific requirements.
The process begins with the design of a mold, which is usually created using advanced computer-aided design software. Once the mold is fabricated, raw materials are warmed until they become molten and then injected into the mold at high pressure. After cooling and solidification, the mold is released, and the final part is ejected. This method facilitates the efficient production of intricate shapes and features, leading to minimized material waste and decreased costs over time.
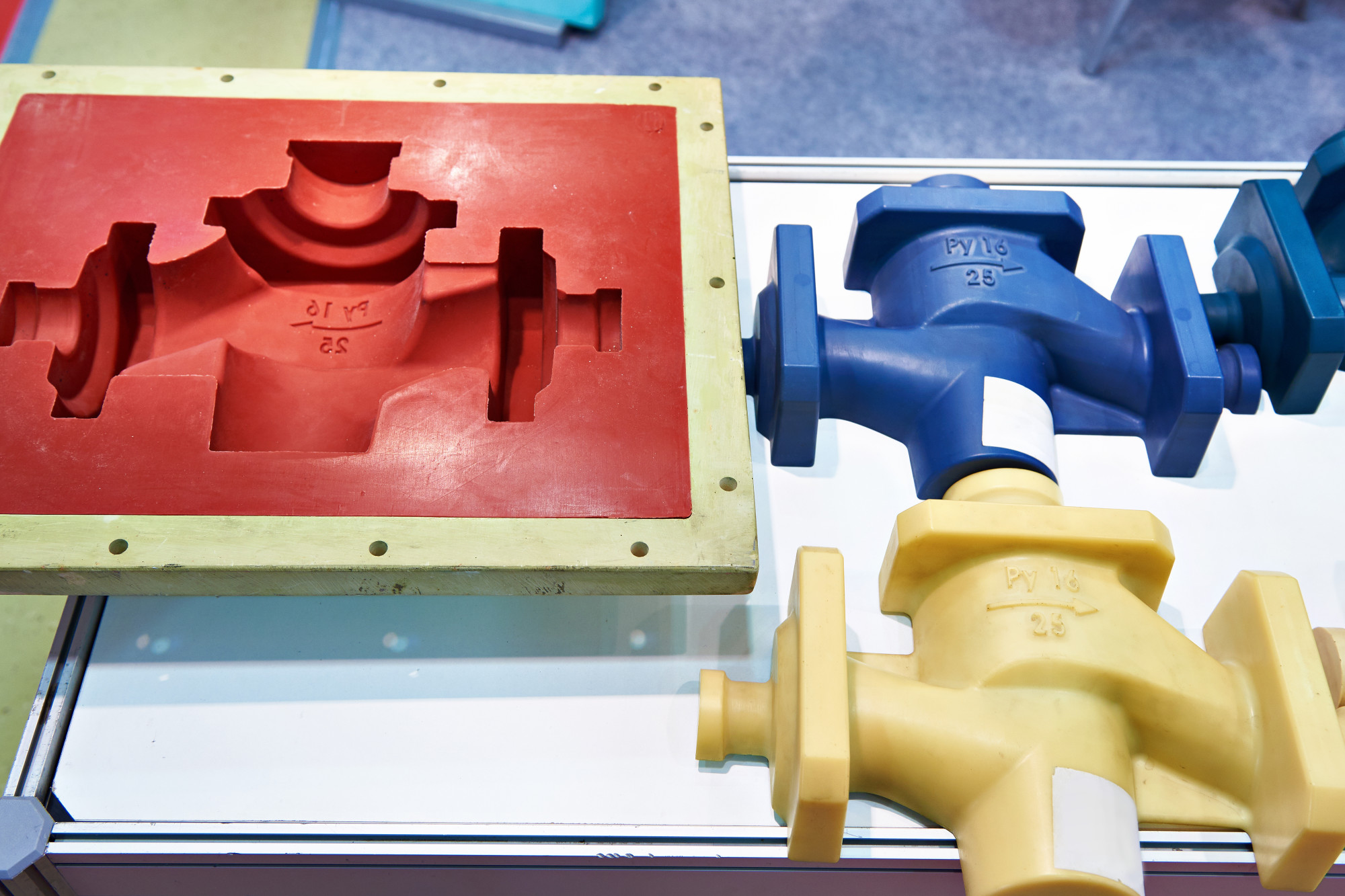
This type of molding is particularly advantageous for businesses looking to increase production or create unique components that vary from mass-produced items. By designing molds tailored for a client’s needs, manufacturers can enhance products for functionality, design, and performance. This level of customization ensures that companies can fulfill their market demands while maintaining high quality and reducing lead times.
Gains of Personalized Press Forming
Tailored injection molding offers extraordinary design flexibility, allowing manufacturers to create intricate geometries and detailed shapes that would be difficult or not possible to achieve with alternative methods. This capability enables the production of parts with exact dimensions and complex features, ensuring consistency in quality and performance. Additionally, the use of advanced materials in tailored injection molding can boost product life span and functionality, catering to specific industry needs.
Another notable advantage of personalized injection molding is its productivity in high-volume production. Once the initial mold is created, the process enables rapid output of large quantities of identical components, lowering production time and labor costs. This efficiency not only hastens time-to-market for new products but also leads to substantial cost savings, making it a extremely economical choice for businesses looking to scale their operations successfully.
Lastly, personalized injection molding promotes green practices through material optimization and minimized waste. The process allows for careful control over material utilization, minimizing excess and scrap. Furthermore, manufacturers can choose green materials and include recycled content, aligning their production with increasing environmental standards and consumer demand for sustainable methods. This commitment to eco-friendliness not only supports the environment but can also boost a company's brand reputation in the marketplace.
Utilization of Tailored Injection Molding
Custom injection molding finds its use across a varied range of sectors, showcasing its flexibility and productivity. In the vehicle sector, manufacturers rely on this technique to produce complex components such as instrument panels, lighting enclosures, and engine shrouds. The ability to shape materials into precise shapes allows for better performance and durability, which is critical in the highly competitive automotive market.
A different significant area where bespoke injection molding excels is in consumer electronics. Devices such as smartphones, tablets, and wearable technology utilize molded pieces for their casings and inner parts. The precision of bespoke molding ensures that these parts connect seamlessly together, providing consumers with attractive and practical products. Furthermore, the quick prototyping capabilities allow manufacturers to innovate quickly and respond to market changes effectively.
Healthcare is yet another field that benefits immensely from custom injection molding . Medical devices and components, such as syringes, inhalers, and diagnostic equipment, often require close conformity to safety and quality standards. Tailored molding not only meets these stringent requirements but also allows for the production of lightweight, long-lasting, and biocompatible parts. This ensures that medical products are not only efficient but also reliable for use in sensitive applications.